In cost accounting, process costing plays a pivotal role in determining the cost of production in industries characterized by mass production or continuous processes. This method enables businesses to allocate costs accurately, making informed decisions and setting appropriate pricing strategies. Let’s explore process costing, its definition, key concepts, and the step-by-step process involved.
Definition of Process Costing
Process costing is a cost accounting method which helps determine the total cost of production in industries where goods are produced in a continuous or repetitive process. This method is particularly suitable for industries like food and beverage, chemicals, textiles, and electronics, where the production process consists of a series of interconnected stages.
Click here to Know the Difference Between Cost Accounting and Management Accounting.
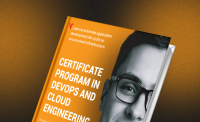
Get curriculum highlights, career paths, industry insights and accelerate your technology journey.
Download brochure
Important Concepts in Process Costing
Process costing is a method of assigning costs to products or services as they move through various stages of a production process. It’s a crucial accounting technique used in industries where products are manufactured in a continuous flow, such as chemicals, textiles, food processing, and more. Understanding the important concepts in process costing is essential for accurate cost allocation and effective financial management. Here are some key concepts:
- Equivalent Units: Equivalent units represent the partial completion of units in a production process. Since not all units are completed simultaneously, equivalent units help convert partially completed units into an equivalent number of fully completed units, making it easier to allocate costs accurately.
- Direct Material Costs: These are the costs associated with the raw materials used in the production process. Direct material costs are assigned to units based on the quantity of materials used.
- Direct Labor Costs: Direct labor costs refer to the wages paid to workers directly involved in the production process. These costs are assigned to units based on the labor hours worked on each unit.
- Overhead Costs: Overhead costs include indirect costs such as factory utilities, maintenance, supervision, and other operational expenses. These costs are allocated to units using predetermined rates or allocation methods.
Cost Accumulation in Homogeneous Production
Cost accumulation in homogeneous production refers to systematically gathering all relevant costs within a production process involving similar or nearly identical stages. In industries where products go through comparable steps, like assembling electronic devices, this concept ensures that costs are collected accurately for each phase. By recognizing the similarities in these stages, businesses can allocate costs more fairly, providing a clearer picture of production expenses and aiding in decision-making and pricing strategies.
Equivalent Units of Production
Equivalent units of production represent the way partially completed units are measured in terms of fully finished units. In process costing, where products move through multiple stages, some units might be in various stages of completion. Calculating equivalent units accounts for this variability and helps determine the overall progress of production. This concept is vital for accurate cost allocation since it ensures that fully and partially completed units are appropriately considered when calculating costs, providing a more realistic representation of production efficiency and expenses.
Here are the Top 20 Financial Accounting Terms That You Should Know.
Cost Allocation Methods
Two common methods used in process costing are the weighted average method and the FIFO (First-In-First-Out) method. The weighted average method calculates the average cost of all units produced during a period, while the FIFO method assigns the cost of the oldest units first before moving on to the more recent ones.
Understanding the Process Costing Method
Let’s break down the step-by-step process of process costing:
Step 1: Identifying Cost Centers and Processes
The production process is broken down into different cost centers and processes in this initial step. A cost center is a specific stage or area where costs are incurred, like material preparation, assembly, or quality control. By identifying these cost centers, businesses can track how resources are used at each stage and ensure that costs are attributed correctly.
Step 2: Accumulating Direct and Indirect Costs
Direct costs like raw materials and direct labor, can be directly traced to a specific cost center. Indirect costs, also known as overhead costs, are not directly tied to a particular stage but contribute to the overall production process. These costs are allocated to cost centers using predetermined allocation methods, such as machine hours or labor hours. This step ensures that all direct and indirect costs are considered when determining the total production cost.
Step 3: Calculating Equivalent Units
Production processes often involve units that are at different stages of completion. Some might be partially finished while others are fully completed. Calculating equivalent units takes this into account. It’s like expressing the partially completed units as fully finished units. This calculation helps determine the overall progress of production and ensures that both partially and fully completed units are considered when calculating costs.
Step 4: Assigning Costs to Finished Units
Once the accumulated costs are determined and equivalent units are calculated, the next step is to assign costs to fully completed units. The total accumulated costs are divided by the equivalent units to calculate the cost per unit. This cost is then assigned to each fully completed unit, providing an accurate view of the total cost of production.
Use of Process Costing
Process costing is widely used in industries where products are produced through a continuous and repetitive manufacturing process. This method of cost allocation is particularly suited for situations where products are indistinguishable from one another, making it challenging to assign costs to individual units. Here are some common uses of process costing:
Chemical Industry: Process costing is extensively used in the chemical industry, where raw materials undergo various chemical reactions and transformations to produce different chemical products. The costs associated with mixing, processing, and refining are allocated to the output based on equivalent units.
Food and Beverage Industry: In industries like food processing and beverage production, where ingredients are mixed and processed in a continuous flow, process costing helps track costs related to ingredients, labor, and other resources involved in creating finished goods.
Textile Industry: Textile manufacturing involves multiple stages, from spinning to weaving to dyeing. Process costing is utilized to allocate costs at each stage, considering both direct costs (materials and labor) and indirect costs (utilities, maintenance, etc.).
Oil and Gas Refining: Refineries process crude oil into various petroleum products. Process costing is used to distribute costs across different products, such as gasoline, diesel, and jet fuel, as they move through refining stages.
Pharmaceutical Industry: Pharmaceuticals often require complex processes and precise measurements. Process costing helps track the costs associated with producing drugs and pharmaceuticals, ensuring accurate pricing and cost control.
Paper Industry: Paper manufacturing involves multiple processes, including pulping, drying, and cutting. Process costing is employed to determine the costs incurred at each stage, leading to an accurate valuation of finished paper products.
Automobile Manufacturing: In automobile assembly lines, process costing is used to allocate costs related to various production stages, such as welding, painting, and assembly, to different vehicle models.
Conclusion
In this guide, we have learned all about process costing. Process costing is a valuable tool in cost accounting, particularly for industries that engage in continuous or repetitive production. By breaking down the production process into manageable stages and accurately allocating costs, businesses can gain insights into their production efficiency, make informed pricing decisions, and enhance overall cost management.
FAQs
Process costing is a method of assigning costs to products or services as they move through various stages of a production process. It's a crucial accounting technique used in industries where products are manufactured in a continuous flow, such as chemicals, textiles, food processing, and more. Understanding the important concepts in process costing is essential for accurate cost allocation and effective financial management.
The process includes:
- Identifying Cost Centers and Processes:Different stages of production are identified as separate cost centers. These can be distinct areas or phases where materials and labor contribute to the final product.
- Accumulating Direct and Indirect Costs:Direct costs like materials and labor are assigned directly to cost centers. Indirect costs, such as overhead, are allocated using predetermined methods like machine hours or labor hours.
- Calculating Equivalent Units:This step accounts for units at various stages of completion. Equivalent units reflect the number of fully completed units that could have been produced with the effort and resources used on partially finished units.
- Assigning Costs to Finished Units:Total accumulated costs are divided by equivalent units to calculate the cost per unit. This cost is then assigned to fully completed units, giving a comprehensive view of production costs.
There are various costing methods, including job costing, process costing, activity-based costing (ABC), and standard costing.
ABC analysis, or Activity-Based Costing, is a method that identifies the activities that consume resources and assigns costs accordingly, providing a more accurate view of cost distribution.
A cost sheet is a document that outlines the various costs involved in producing a product, including materials, labor, and overhead costs.
The basic principles of costing include the identification and classification of costs, allocation of costs to cost centers, determination of cost behavior, and analysis of cost-volume-profit relationships.
Process costing simplifies the intricate task of cost allocation in industries with complex production processes. By understanding its concepts and implementing its methods, businesses can navigate the realm of cost accounting with confidence and precision.