In the dynamic landscape of production, ensuring top-notch quality control has become paramount. The pursuit of excellence not only safeguards a company’s reputation but also guarantees customer satisfaction.
Mastering quality control involves meticulously monitoring, assessing, and refining products or services. This intricate practice demands a fusion of advanced technologies, streamlined methodologies, and a dedicated workforce.
By upholding rigorous quality standards, businesses can forge a strong competitive edge while cultivating unwavering consumer trust.
In the section below, we’ll into the art of mastering quality control, unveiling its significance and the transformative impact it holds across industries.
Conquering Quality Control: Techniques for Consistency and Perfection
In the intricate realm of production, “quality control” emerges as the guardian of excellence, ensuring that each product that leaves the assembly line meets predefined standards.
This meticulous process is more than just a routine; it’s a commitment to delivering unparalleled quality. Through systematic checks, adjustments, and fine-tuning, businesses achieve the pinnacle of “assurance of quality.”
By employing cutting-edge technologies and expert techniques, they strive for consistency in every batch and perfection in every detail.
In this journey of “quality control” mastery, industry players unlock the power to elevate their brand’s reputation, foster customer loyalty, and stand out in the market.
Learn more about Strategic management process: Meaning & Steps.
Precision Matters: The Role of Quality Control in Delivering Superior Products
Imagine a world where every manufactured item is flawless, where “assurance of quality” is not just a phrase but a fundamental principle. This is where “quality control” steps in, assuming a pivotal role in pursuing perfection.
Its significance lies in meticulously crafted processes that leave no room for errors, ensuring “assurance of quality” at every step. From raw materials to the finished product, each stage is under the vigilant eye of quality control experts.
Through stringent tests, measurements, and evaluations, businesses secure the precision that underlines their commitment to delivering “superior products.”
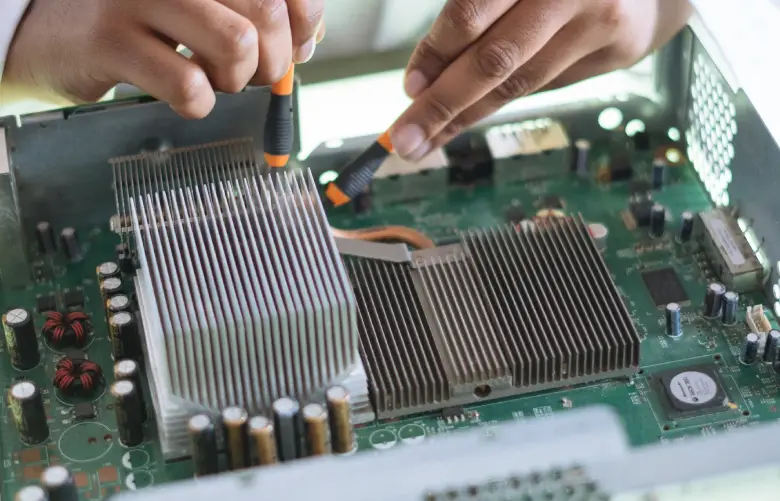
This role doesn’t just shape products; it shapes reputations and builds trust, solidifying the bond between businesses and their valued customers.
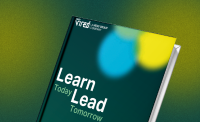
Get curriculum highlights, career paths, industry insights and accelerate your management journey.
Download brochure
Quality Control Unveiled: Strategies for Maintaining High Standards
Here’s a breakdown of how to maintain high standards through quality control:
Integrated Inspection Protocols
- Regularly assess raw materials, components, and final products to uphold “quality control.”
- These protocols enhance the “assurance of quality” by identifying issues early.
Precision Measurements and Testing
- Conduct thorough tests, such as stress tests or performance evaluations, to ensure the highest “assurance of quality.”
- Accurate measurements and rigorous testing leave no room for discrepancies.
Data-Driven Analysis
- Make informed decisions based on this analysis to improve “quality control” processes.
- Data-driven insights contribute to the ongoing enhancement of “assurance of quality.”
Continuous Process Improvement
- Encourage feedback from front-line workers to enhance the “assurance of quality.”
- Iterative refinements keep products in line with evolving standards.
Training and Skill Development
- Equip them with the necessary skills to contribute to effective “quality control.”
- Skilled and knowledgeable employees play a crucial role in maintaining the “assurance of quality.”
Collaboration and Communication
- Collaborate on addressing quality control issues promptly to strengthen “assurance of quality.”
- Transparent communication ensures alignment towards shared quality goals.
Here is a detailed guide on How to Ace a Supply Chain Management Interview.
Beyond Perfection: Navigating the Realm of Quality Control
Quality control is more than ensuring a product’s flawlessness; it’s about navigating a comprehensive landscape of meticulous processes and unwavering commitment.
In this journey, “assurance of quality” becomes the guiding light, guiding businesses towards excellence and customer satisfaction.
Here’s a closer look at what it means to navigate the realm of quality control:
Exploring Multi-Faceted Processes
Quality control entails a series of systematic steps designed to maintain standards and enhance the “assurance of quality.” Every stage is meticulously orchestrated from sourcing raw materials to final inspections to ensure that products meet or exceed expectations.
Precision Amid Complexity
In the intricate web of manufacturing, quality control brings precision to complexity. It involves meticulously examining details, measurements, and parameters, all aimed at achieving the highest “assurance of quality.”
Continuous Vigilance and Adaptation
Navigating quality control requires constant vigilance. As industries evolve and customer demands change, businesses must adapt their “assurance of quality” strategies. Continuous monitoring, analysis, and improvement ensure that products remain consistent and reliable.
Trust-Building Beyond Perfection
Quality control is more than achieving perfection; it’s about building trust. Customers rely on the “assurance of quality” to make purchasing decisions.
By consistently delivering products that surpass expectations, businesses earn and retain customer trust in an increasingly competitive market.
Here’s a breakdown of how quality control is demystified through various tools and approaches:
Control Charts for Continuous Monitoring
- Control charts visually display process variations over time.
- They help identify trends, outliers, and abnormal variations that may affect quality
Root Cause Analysis
- When issues arise, SPC aids in identifying the root causes of deviations.
- Pinpointing the source allows for targeted corrective actions, preventing future occurrences.
Process Capability Analysis
- SPC assesses a process’s capability to produce products within specifications consistently.
Six Sigma Methodology
- Six Sigma combines SPC with process improvement techniques.
- It aims for near-perfect processes, reducing defects and variations to a minimum.
Lean Principles Integration
- Lean principles complement SPC by minimizing waste and optimizing processes.
Continuous Improvement Culture
- Quality control is a dynamic process that thrives on continuous improvement.
Quality Control Chronicles: From Traditional Methods to Modern Best Practices
Standardization of Processes
Quality control is standardizing processes across the production cycle. This entails establishing consistent procedures and protocols applied uniformly at every manufacturing stage. By adhering to these standards, companies make sure that products are produced consistently, minimizing variations that could compromise quality.
Continuous Monitoring
Continuous monitoring allows companies to swiftly identify anomalies, intervene promptly, and rectify issues before they escalate. This real-time vigilance ensures that products maintain the desired quality levels and prevents defects from propagating.
Data-Driven Insights
By systematically gathering data throughout the production journey, businesses can gain valuable insights into trends, patterns, and potential areas of improvement. These insights inform decision-making, enabling proactive adjustments and enhancements that result in refined product quality.
Error Prevention over Detection
By identifying potential sources of errors and implementing preventive measures, companies can avoid costly rework, reduce waste, and maintain a higher level of consistent quality.
Employee Involvement and Training
Engaging employees in the quality control process is integral to its success. Empowering staff to contribute their insights and expertise fosters a sense of ownership and responsibility.
Providing thorough training equips employees with the skills necessary to identify issues and maintain quality standards. When actively involved and trained, employees become valuable assets in upholding product excellence.
Customer-Centric Approach
By consistently delivering products that meet or exceed customer expectations, companies cultivate loyalty, build trust, and establish themselves as reliable sources of high-quality goods.
Process Improvement Culture
Regularly assessing processes, identifying areas for refinement, and implementing changes in response to evolving demands create a dynamic environment where product quality constantly evolves and improves.
Root Cause Analysis
Addressing quality issues at their root is a critical principle. Instead of addressing surface-level defects, businesses analyze root cause to identify the underlying reasons for problems.
Companies can prevent recurring issues by treating the cause rather than the symptoms and bolster long-term product quality.
Risk Management
A proactive approach to risk management is integral to quality control. Identifying potential risks impacting product quality and implementing mitigation strategies mitigates the likelihood of quality deviations.
This principle ensures that unexpected factors are considered and managed, safeguarding the integrity of products.
Transparency and Communication
Open communication and transparency across all departments involved in production are pivotal in quality control. Sharing information, insights, and updates ensures everyone is aligned to maintain consistent quality standards.

Transparency enhances collaboration, reduces misunderstandings, and promotes a shared commitment to delivering high-quality products.
Conclusion
Mastering quality control is a linchpin for sustained success in the ever-evolving business landscape. By embracing advanced methodologies, data insights, and a commitment to continuous improvement, companies forge a path to excellence.
Quality control isn’t just a process; it’s a pledge to customers, a catalyst for growth, and a cornerstone of enduring success.
To implement these top-notch practices that aid “assurance of quality” in your professional life, check out Hero Vired’s Product Management course certification here!
FAQs
Quality control is a systematic process which ensures products or services meet predetermined standards of excellence.
Quality control's key principles encompass standardized processes, continuous monitoring, data-driven insights, error prevention, employee involvement, customer focus, process improvement, root cause analysis, risk management, and transparent communication. All of these contribute to the overall assurance of quality.
Quality control professionals are responsible for ensuring that products meet established quality standards. Their role includes proactive monitoring, identifying deviations, and implementing corrective actions to maintain consistent quality.
Quality control benefits many industries, including manufacturing, healthcare, automotive, food and beverage, electronics, pharmaceuticals, construction, etc.
A successful quality control system is built through defined standards, standardized processes, data utilization, employee training, continuous improvement, technology integration, customer feedback, collaboration, audits, and adaptability.