In today’s business’s dynamic, rapidly changing environment, meeting operational efficiencies on a bar-flying production line alongside product safety and regulatory compliance is paramount. Quality Risk Management (QRM) is a systematic approach to evaluating, identifying, measuring and controlling identified risks whose occurrence may affect quality, safety or regulatory compliance. Embedding QRM in their processes empowers organisations to further improve their operational performance, increase resource utilisation, minimise risks, and build consumer trust in their products to ensure they meet the highest levels of quality and compliance.
What is Quality Risk Management?
Quality Risk Management (QRM) is a structured and systematic process in which we determine, assess, control, communicate and follow up on product quality risks while the product is in its life cycle. This approach addresses potential risks at the earliest stage, performs due diligence in-depth analysis and mitigates them up to levels that are considered acceptable while maintaining full conformity to regulatory standards. QRM enables organisations to proactively address risks to maintain high-quality products and protect consumers in a more complex and regulated environment.
Key Objectives of QRM:
- Protect Product Quality, Patient Safety, and Data Integrity: Keeping the quality level, safety regulations and the accuracy and confidentiality of critical data was maintained. In contrast, the final product is ensured to meet quality standards.
- Enhance Decision-Making with a Science-Based and Data-Driven Approach: Using data and scientific analysis to make responses that effectively mitigate and improve processes using data and scientific analysis.
- Reduce the Likelihood of Failures, Inefficiencies, or Regulatory Breaches: Helps proactively identify risks and mitigate to minimise the likelihood of operational failures, delays or regulatory violations.
Also Read: Risk Analysis in Financial Management
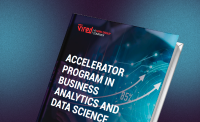
Get curriculum highlights, career paths, industry insights and accelerate your finance journey.
Download brochure
Why is Quality Risk Management Important?
Organisations must have Quality Risk Management (QRM) to increase process efficiency, ensure product safety, and ensure regulatory compliance. Those industries where safety is absolute, and there is an extreme stringency of the regulation will pay catastrophic consequences if risk management is not considered. QRM works to meet consumer expectations, control for potential failures, and keep competing by proactively addressing potential risks. Here’s how it adds value:
- Optimise Resources: QRM helps businesses focus on the highest-risk activities, eliminating unnecessary spending, time and effort. Doing that ensures that resources are allocated to areas that will most effectively reduce risk and improve the processes.
- Ensure Compliance: QRM-adopted practices result in organisations maintaining ongoing compliance with important regulatory standards, such as GMP (Good Manufacturing Practices), ISO, and FDA guidelines. Organisations gain by identifying risks and managing them to avoid costly fines, legal issues and delays occasioned by non-compliance.
- Build Consumer Trust: Organisations can create and reinforce consumer trust by consistently supplying high-quality, reliable products. Increased consumer demand for transparency and quality assurance requires organisations to keep their reputation and customer loyalty through QRM.
Also Read: Top Interview Questions for Risk Management
Core Principles of Quality Risk Management
Quality Risk Management (QRM) is based on systematic processes that evaluate and control product quality, safety or regulatory compliance risks. The following core principles guide the successful implementation of QRM:
Risk Identification
In the first step of QRM, risks that could impact product quality, patient safety or regulatory compliance are identified. Performing this process requires a high level of detail and analysis, from mapping the processes to identifying hazards to documenting the potential sources of risk. Documentation is a must to track risks thoroughly so that all possible threats are acknowledged and taken care of early on. The building of effective risk management strategies begins with proper risk identification.
Risk Assessment
However, after identifying risks, the next step is to rate them based on whether they are likely and what they might impact. Risk assessment helps organise risks so organisations can spend their resources better on those threats that matter most. Tools commonly used in risk assessment include:
- Failure Mode and Effects Analysis: This tool aims to identify failure points in systems and processes that lead to consequences and enable a risk prioritisation strategy.
- Hazard Analysis: Hazard analysis is often used in manufacturing and healthcare-oriented industries to assess the risk of a specific process, machinery or system. The result of this analysis can help identify potential hazards and their magnitude and thus help with targeting the risk control measures.
Risk Control
The risk can be reduced or eliminated by taking proactive risk control steps. It might include putting preventive steps in place, providing controls to handle risk exposure, and continuously monitoring the effectiveness of controls. Having risk control guarantees an acceptable level of risk over time and controls them as they occur. Revising procedures, using engineering controls, and adding new technology to ensure regulatory compliance and maintaining product quality are all included.
Risk Communication
QRM requires communication since all stakeholders need to know the current risks identified, the measures in place to control the risk, and what actions are being taken to mitigate the risks. Finding a balance of regular communication across the entire organisation heightens transparency; thus, everyone knows their roles in managing risk. Vertical and horizontal accountability of the RQM is meaningful and interpretable only if management and the workforce clearly and consistently understand what is expected of them to attain QRM.
Risk Review
QRM is an iterative, ongoing process. Perhaps most importantly, risks, controls and processes must be reviewed regularly to ensure they are still working amid ever-changing situations. The neat thing with theories on continuous improvement is that periodic reviews and updates are in order in case new data sets, regulatory changes, or unforeseen developments arise. By continuously monitoring risks, organisations can quickly adapt and respond to changes, and the risk management process is dynamic and responsive to new challenges.
Also Read:
Several tools and techniques are used in effective quality risk management, such as risk assessment, control, and mitigation. These tools allow organisations to systematically address potential problems in product quality, safety, and regulatory compliance. Below are some key tools commonly used in QRM:
Failure Mode and Effect Analysis
FMEA can identify potential items of failure in a process and evaluate the potential, likelihood, and detectability of failure for such items. This structure allows it to help prioritise by creating a systematic approach to analysing critical failures for each process step.
Hazard Analysis Critical Control Point
HACCP is common in food and pharmaceutical industries and involves finding critical control points in production. It manages the points at hand, ensures product safety is well managed, and minimises product hazards.
Ishikawa Diagram (Fishbone Analysis)
This tool will show you the root causes of quality issues. It helps teams categorise (People, Processes, Equipment,) which enables them to narrow down potential problems on what to focus on.
Fault Tree Analysis (FTA)
FTA is a top-down method that looks at potential system failure. It neatly maps out failure paths and provides means to identify critical vulnerabilities in complex systems and prioritise preventive actions.
Risk Matrix
A risk matrix is a useful way of evaluating and prioritising risk, considering the probability and impact of each risk. It is categorised into a category (e.g., low, medium, high) for good risk management.
Monte Carlo Simulation
This technique employs statistical methods to model and predict outcomes of uncertain events for areas such as risk scenario assessment, an organisation’s ability to assess the likelihood and impact of different risk scenarios.
Root Cause Analysis (RCA)
RCA identifies the underlying causes of problems in a system. The primary aim is to identify the key reasons for an issue that should be implemented.
Steps to Implement Quality Risk Management
Placing into practice Quality Risk Management (QRM) means a methodically drawn-out procedure for assessing the risks and ensuring product quality, safety and regulatory compliance. Below are the key steps for implementing an effective QRM framework:
1. Establish Objectives
To be effective, the first step is to define the goals and scope of the QRM activities so that they fit with the organisation’s stake in the end. The goal may be to improve product quality, follow regulatory standards or limit safety risks.
2. Choose a cross-functional team.
Guarana involves people from different departments in the company, such as quality control, operations, compliance, and product development. Your diverse team has varied perspectives and experiences so you won’t miss anything with risk – you have covered it from all angles.
3. Risk Assessment
You must perform a thorough risk assessment to locate potentially harmful hazards or risks to your product’s quality or safety. The likelihood and impact of these risks can be evaluated and ordered based on tools like FMEA (Failure Mode and Effects Analysis) or HACCP (Hazard Analysis and Critical Control Points).
4. Design Risk Mitigation Plans
Identify risks and prioritise and develop a detailed risk mitigation plan for each. These plans should include specific actions and controls to reduce or reduce the present identified risks. Instead, there should be an emphasis on managing high-priority risks that substantially impact product quality or compliance.
5. Implement Control Measures
You put those risk mitigation plans into action by implementing control measures. Process changes, new equipment, training and better quality assurance protocols might all be used here. Concerning risk reduction, reducing risks effectively depends on the appropriate application of these measures.
6. Monitor and Review
That is, risk management is an ongoing process. Identify controls and objectives (key risk indicators) and then continuously monitor the effectiveness of what has been implemented through audits, inspections, and performance metrics. Review and update the risk management plans regularly and as needed to include new risks, regulatory changes or technological improvements.
7. Documentation and Reporting
Keep good documentation of all risk management activities, from risk assessments and mitigation plans to ongoing reviews. This documentation serves as a compliance reference and will be valuable during audits or regulatory inspections to verify that the QRM process is effective.
Also Read: A Detailed Guide to the 5-Step Risk Management Process
Benefits of Quality Risk Management
Several valuable advantages, not to mention product safety and search, result from the well-thought-out implementation of a robust Quality Risk Management (QRM) framework, enabling businesses to improve internal processes, achieve more business performance, and comply with regulatory requirements. Here are some of the key benefits:
Improved Product Quality
QRM recognises that the early identification and solution of possible risks in production will ensure that products always meet or exceed industry standards. The emphasis on quality helps organisations bring real products to the market that are safe and reliable, thus avoiding defects and recalls.
Operational Efficiency
People prefer to structure the QRM approach because it helps prioritise risk areas, allowing the organisation to focus on where the resources are needed. The prioritisation within this means that operation will be more streamlined, waste and inefficiencies will be reduced, and resource allocation will be optimal.
Regulatory Compliance
Industries such as pharmaceuticals, food and healthcare are highly ISO and GMP compliant, requiring strict adherence to standard regulations. Such a QRM framework for businesses is established, eliminating the risk of expensive fines, penalties or a product recall. At the same time, it helps with timely reporting and documentation for inspections and audits.
Enhanced Decision-Making
QRM bases its assessment on assessment using data-driven and science-based risk evaluation, allowing one to make objective and appropriate decisions. It eliminates guesswork or subjective judgement of decisions made during the production, development and risk management processes and results in more consistent, better quality decisions.
Increased confidence of Stakeholders
Organisations committing to risk management and regulatory compliance will boost customer, regulator, investor, and business partner trust. The company’s strong QRM practices represent the dedication to discovering and implementing the best ways of responding to situations that can lead to safety issues, quality issues, or insufficient operational resilience.
Proactive Risk Mitigation
QRM offers businesses a chance to look for potential risks before they come real and take preventive measures. By dealing with risks beforehand, they can mitigate or prevent costly disruptions and lessen the impact of issues.
Continuous Improvement
However, QRM strategies are a continuous process of monitoring and reviewing risks, keeping their evolving momentum in line with changing market conditions, new regulations, and new technologies. Organisations are supported by this dynamic approach to ensuring that they remain ahead of potential risks and respond to industry developments, thereby nurturing the potential for long-term resilience.
Challenges in Implementing QRM
The benefits of implementing Quality Risk Management (QRM) far outweigh the challenges, but a number exist that need to be navigated by organisations. Unsuccessfully addressed challenges can impede the QRM framework application. Below are some of the key obstacles organisations may face:
Complexity of Processes
Mapping and analysing complex, interconnected organisational processes make up most QRM cases. You must completely understand how different systems function and interact to do this. Such diversity across these processes means that the time identifying potential risks is often long, and expertise is needed. However, the challenge is breaking down complex systems into manageable parts for evaluating risk.
Resource Intensive
QRM does require a large investment in human and technical resources. To do this, you must have the means to evaluate and manage risks with skilled personnel, specialised tools, and enough time. The framework should be implemented and maintained effectively in ways organisations must train employees and hire experts. These necessary investments can be difficult for smaller organisations (or organisations with too little cash) to make.
Resistance to Change
Introducing new risk management practices can be difficult, especially in organisations where systems are established and deeply embedded. New tools and methodologies employees are unfamiliar with or afraid of ‘sticking a finger in’ may be hard to adopt. To overcome this resistance, effective change management, communication, and leadership must be in place to gain active buy-in from everyone on the team.
Continuous Monitoring
Finally, a good QRM system is only good if it’s monitored. Risks change with new technologies, regulations, and market dynamics. These changes should be accommodated through regular reviews and updates to risk management plans. Maintaining a strong QRM system is continuously resource-intensive and challenging to keep up over time.
Industries Benefiting from QRM
Quality Risk Management is important in industries that dictate the need to be safe, compliant, and adhere to regulations. The following industries particularly benefit from implementing QRM frameworks to safeguard operations, reduce risks, and ensure compliance:
Manufacturing
Most manufacturing processes are complex, with machinery, assembly lines, and product specifications, each having risks. QRM achieves these production efficiency improvements, defect reduction, and product reliability. Proper risk identification and handling leads to the optimisation of the manufacturer’s operations, a reduction of downtime, and an increased quality of products.
Healthcare
Medical procedures, sustaining and caring for patients, and device usage could lead to tremendous risks in healthcare. QRM controls the risks of hazards by systematising and controlling potential hazards. Healthcare organisations use QRM to ensure Qpid streamlines care protocols, improves patient safety, and ensures that medical devices and treatments meet stringent regulatory standards. This is far more important to prevent errors during patient care or medical procedure delivery.
Pharmaceuticals
It is a heavily regulated pharmaceutical industry with heavy regulations about drug development, production, and safety. It (QRM) is critical to ensure that products are safe and effective and meet all regulatory requirements (GMP) for Good Manufacturing Practices. Pharmaceutical companies are offered the method of systematic risk management that can ensure track quality, patient safety, and industry standards.
Food and Beverage
Safety and quality have to be very on point in food and beverage. QRM, like HACCP (Hazard Analysis and Critical Control Points), supports food safety standards to ensure risk at critical control points in production. It ensures food safety, lowers the contamination hazard, and upholds the regulatory requirement of food labelling and processing.
Future of Quality Risk Management
With technological advancements, QRM is evolving to include predictive analytics, artificial intelligence, and automation. These tools enable real-time monitoring, faster risk identification, and more precise mitigation strategies. QRM will become more proactive as industries grow increasingly data-driven, helping organisations address risks before they materialise.
Conclusion
The QRM is concerned with rules, regulations, and implementation to attain operational dimensions and product excellence in different organisations. This paper posits that organisations can minimise risks, protect products, adhere to regulatory compliance, and amplify process improvement, all through the use of an effective risk management framework that is particular and orderly. QRM is most effective in industries with potentially negative risks, such as safety, quality, and efficiency, including pharmaceuticals, manufacturing, and healthcare.
In conclusion, the times business practising the approach of QRM not only protects their business but also increases the chances of continuously serving high-quality products that would meet the expectations of the existing or new consumer. Get to know about all the risks in finance and how to manage them with the Certificate Program in Financial Analysis, Valuation, & Risk Management with EdX by Hero Vired.
FAQs
Quality risk management is a systematic and risk-based approach to quality management. Quality risk process comprises assessment, control, communication and review of quality risks. However, as critical as the need is in the pharmaceutical industry, where product quality can impact consumer health and safety, the need is even higher in those industries with products that pose direct threats to the surroundings.
Regarding quality assurance (QA) in the form of risks, they’re the “what ifs,” the negative effects that will happen to us or that can come our way. It’s a blend of how bad something is and how much it can mess us up if it does:
The basic ideas of quality management principles are considered true, and quality management principles' basic ideas can serve as a basis for quality management. The QMPs can be used to build a basis for a system's systems.
Organisations must know the overall risk level embedded in their processes and activities. In ISO 9001, the risk is the uncertainty of satisfying the system's objectives of providing products and services that meet customers’ requirements.
Active risk is created by actively managed portfolios like mutual funds or hedge funds, attempting to outperform their benchmark. More specifically, active risk is the difference between the return on the managed portfolio minus the return on the benchmark over some amount of time.
Updated on December 4, 2024