Lean manufacturing is a meticulously crafted production approach, stemming from the Toyota Production System, that centers around optimizing processes to achieve remarkable efficiency and effectiveness. At its core, lean manufacturing aims to accomplish two key goals:
Delivery of optimal value to customers: Lean thinking begins by identifying what customers value in a product or service. This helps distinguish between activities that add value and those that don’t.
Waste Elimination: Waste, in the context of lean manufacturing, refers to any aspect of the production process that consumes resources but doesn’t contribute to the final product’s quality, functionality, or value.
What is Lean Manufacturing?
Lean manufacturing is a production methodology developed by the Toyota Production System, aiming to eliminate waste, enhance efficiency, and deliver customer value.
It emphasizes value identification, streamlined processes, pull-based production, and continuous improvement.
Lean manufacturing is a vital strategy and has been widely adopted in various industries beyond automotive, including aerospace, healthcare, and services. It has consistently demonstrated its ability to reduce costs, improve quality, increase productivity, and enhance customer satisfaction.
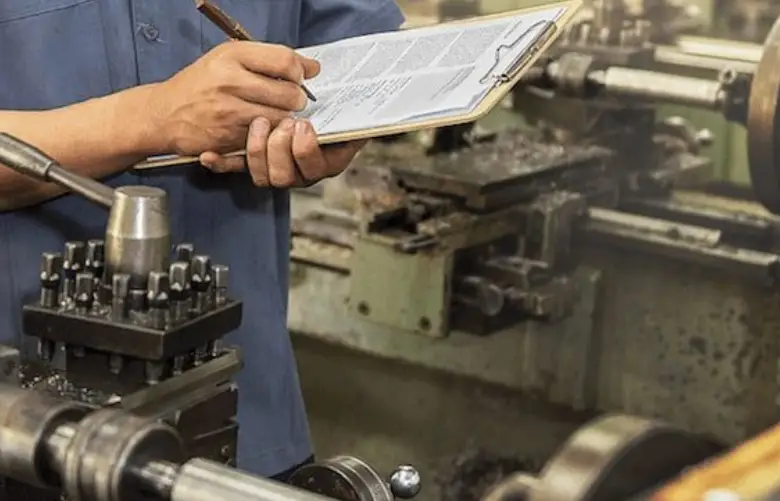
By embracing lean manufacturing principles, organizations can achieve sustainable competitive advantages and adapt to changing market demands.
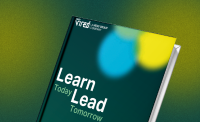
Get curriculum highlights, career paths, industry insights and accelerate your management journey.
Download brochure
The Lean Manufacturing Principles
Continuous Improvement (Kaizen)
Kaizen, one of the lean manufacturing principles, meaning “change for better,” is a foundational principle of lean manufacturing. It involves a relentless commitment to incremental improvements in processes, products, and systems. By encouraging all employees to contribute ideas for enhancement, organizations create a continuous learning and refinement culture.
Value Stream Mapping (VSM)
Value Stream Mapping is a visual lean manufacturing tool used to analyze and optimize the flow of materials and information required to bring a product from its raw material state to the hands of the customer. By identifying bottlenecks, redundancies, and inefficiencies, VSM helps streamline processes and increase efficiency. It facilitates informed decision-making, focusing resources on the most valuable areas.
This in turn aids the lean manufacturing principles and streamlines operations to deliver products and services with higher quality, shorter lead times, and reduced costs.
Identifying and Reducing Waste
Lean manufacturing is key in order to identify and eliminate waste to optimize processes and enhance efficiency. There are eight common types of waste, known as the “8 Wastes of Lean,” that organizations focus on minimizing:
- Defects
- Overproduction
- Waiting
- Non-Utilized Talent
- Transportation
- Inventory
- Motion
- Extra Processing
Lean Tools and Techniques
Lean manufacturing is a process that employs various tools and techniques to identify and eliminate waste while improving processes:
- 5S Methodology
- Kanban
- Single-Minute Exchange of Die (SMED)
- Poka-Yoke
- Total Productive Maintenance (TPM)
- Value Stream Mapping (VSM)
- Continuous Improvement (Kaizen)
- Andon Systems
These tools and techniques aid organizations in pinpointing inefficiencies and systematically reducing waste, ultimately leading to leaner, more efficient operations.
5S methodology
5S Methodology, Kanban Systems, and Poka-yoke (Error-proofing) are three essential concepts in process and quality management.
5S Methodology focuses on workplace organization and efficiency improvement. It comprises five key steps: Sort, Set in order, Shine, Standardize, and Sustain. This methodology enhances productivity and safety by decluttering, arranging items systematically, maintaining cleanliness, setting standards, and ensuring ongoing adherence.
Kanban systems
Kanban Systems are visual tools that aid in managing workflow. Using cards or digital signals, Kanban Systems facilitate real-time tracking of tasks, inventory levels, and production stages. This lean manufacturing technique prevents overproduction, reduces wastage, and maintains a smooth production flow.
Poka-yoke (error-proofing)
Poka-yoke, also known as error-proofing, is a preventive approach to quality management. It involves designing processes and systems in a way that prevents errors from occurring or detects them at an early stage. By implementing sensors, guides, or simple checks, Poka-yoke reduces the likelihood of defects, improving product quality and fewer defects.
Total Productive Maintenance (TPM)
Total Productive Maintenance (TPM) is a comprehensive approach to maintenance of product management that aims to maximize equipment effectiveness and minimize downtime. It involves proactive maintenance strategies, operator involvement, and continuous improvement practices.
Andon systems for real-time problem notification
Andon systems are real-time problem notification tools commonly used in manufacturing environments. They provide a visual signal, such as lights or displays, to alert operators and supervisors about issues on the production floor. This instant notification allows quick response to problems, minimizing delays and improving efficiency.
Lean Manufacturing Implementation
Implementing a Lean Manufacturing system involves adopting streamlined processes to eliminate waste and enhance efficiency. This approach focuses on optimizing value while minimizing resources and time.
Building a Lean Culture
Building a Lean Manufacturing Culture means instilling Lean principles throughout an organization. This requires a collective commitment to continuous improvement and waste reduction.
Employee involvement and empowerment
Employee involvement and empowerment are integral to Lean manufacturing success. Workers’ insights are leveraged to identify inefficiencies, fostering a sense of ownership and accountability.
Leadership’s role in driving lean initiatives
Leadership plays a crucial role in driving Lean initiatives. Product managers set the tone, allocate resources, and provide guidance to ensure the adoption and sustainability of Lean practices.
Training and skill development
Training and skill development are vital components. Employees are equipped with the necessary tools and knowledge to implement Lean manufacturing techniques effectively.
Measuring and Sustaining Lean
Measuring and Sustaining lean processing involves using quantifiable methods to gauge the effectiveness of Lean practices over time.
Key Performance Indicators (KPIs) for Lean Manufacturing
Key Performance Indicators (KPIs) for Lean Manufacturing provide measurable benchmarks for performance evaluation. They offer insights into the efficiency and effectiveness of Lean implementation.
OEE (Overall Equipment Efficiency)
OEE (Overall Equipment Efficiency) is a critical KPI. It quantifies the productivity of machinery and highlights areas for improvement in availability, performance, and quality.
Lead time reduction
Lead time reduction is another essential KPI. It measures the time it takes for a product to move through the production process, directly reflecting process efficiency and customer responsiveness.
Defect rates
Defect rates and inventory turnover are important metrics in assessing operational efficiency and product quality.
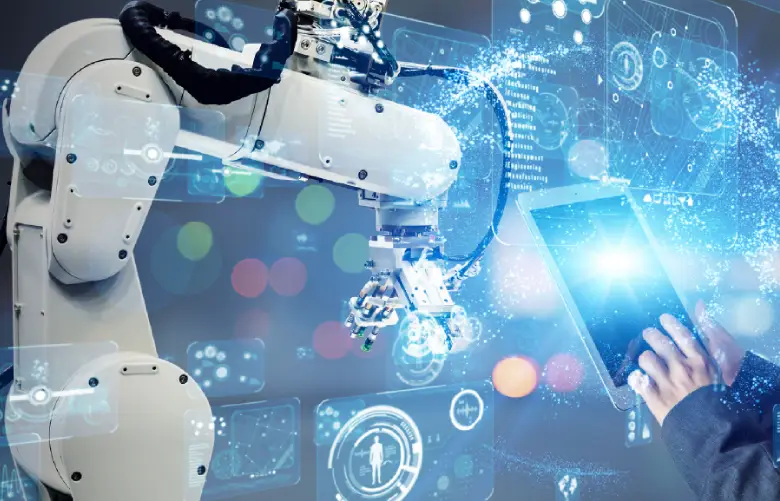
Defect rates indicate the proportion of products that do not meet quality standards. Monitoring defect rates provides insights into the effectiveness of quality control measures and identifies areas for improvement.
Inventory turnover
Inventory turnover measures how quickly inventory is used up or sold within a specific time frame. A higher turnover signifies efficient inventory management, reduced holding costs, and better alignment with customer demand.
Conclusion
The Lean Manufacturing process is a transformative approach aimed at optimizing processes, eliminating waste, and enhancing overall efficiency across industries. By focusing on continuous improvement, employee empowerment, and eliminating non-value-added activities, Lean technology has proven to streamline operations, reduce costs, and elevate product management in 2024. As companies embrace Lean methodologies and a commitment to ongoing improvement, they position themselves to thrive in dynamic markets, deliver exceptional value to customers, and sustain long-term success.
FAQs
The lean process to minimize waste involves identifying and eliminating various types of waste, such as overproduction, waiting times, unnecessary transportation, excess inventory, unnecessary motion, defects, and underutilized talent. This is achieved through systematic analysis, process optimization, and continuous improvement efforts.
Lean manufacturing is effective and increases efficiency by focusing on reducing non-value-added activities and optimizing processes. It emphasizes streamlined workflows, standardized procedures, visual management, cross-functional collaboration, and continuous improvement. By eliminating waste and improving flow, resources are used more effectively, lead times are reduced, and productivity is enhanced.
Lean manufacturing is focused on minimizing waste as a fundamental goal. However, the main purpose goes beyond waste reduction. Lean manufacturing is also a practice that aims to improve overall quality, increase flexibility to meet customer demands, enhance employee engagement, and create a culture of continuous improvement throughout an organization.
Lean manufacturing is a single tool and a comprehensive philosophy and principles aimed at improving workplace efficiency and eliminating waste. It encompasses various tools and techniques, such as 5S, Kanban, value stream mapping, and kaizen (continuous improvement), all working together to create a more efficient and effective operation.
There are numerous lean manufacturing tools, but five commonly used ones are:
- 5S: A workplace organization method to improve efficiency through Sort, Set in order, Shine, Standardize, and Sustain.
- Kanban: A visual scheduling system that helps control inventory levels and improve workflow by signaling when to produce or replenish items.
- Value Stream Mapping: A technique to analyze and visualize the steps and flow of materials and information needed to deliver a product or service to identify areas for improvement.
- Kaizen: A philosophy of continuous improvement that encourages small, incremental changes to processes and systems to achieve greater efficiency and quality.
- Poka-Yoke: Also known as mistake-proofing, this tool aims to prevent errors by designing processes or systems that make mistakes difficult to occur.